Building Success From the Ground Up | Manufacturing Plant Site Selection in DFW
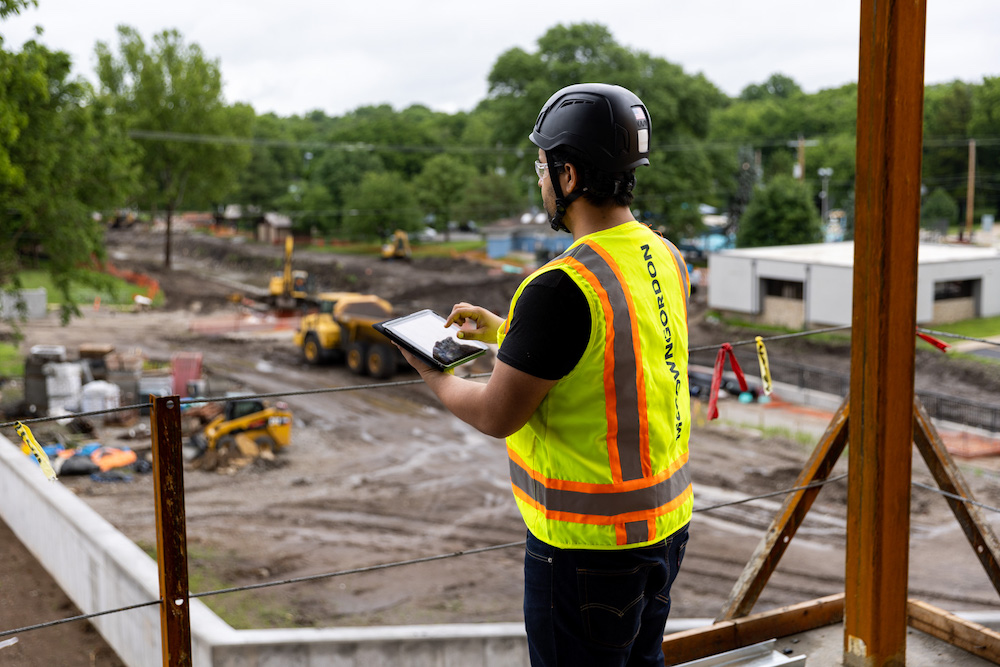
Selecting the right location for your manufacturing plant is crucial to the long-term success of your project. There are many factors to consider with site selection—development costs, availability of utilities, space for future growth, employee demographics and more. Navigating this process can be difficult, but investing time and resources upfront will pay off in the long run.
When you partner with McCownGordon, we’ll guide you through the site selection process from start to finish. As experts in the DFW market, we’ll help you locate the ideal site to support your manufacturing plant for many years to come.
A pulse on Dallas manufacturing plant site selection
In DFW, the manufacturing market is driven by developers. Developers often build out the basics of the facility to a warm shell level (ceilings, lighting, plumbing, HVAC) and then look for food and beverage manufacturing owners to acquire the facility, via lease or ownership. The tenant will then customize the facility based on the specific needs of their product. If you’re a developer, McCownGordon can help with your site selection, design and construction to make it an ideal space for future tenants.
If you’re a manufacturer, McCownGordon can help locate available buildings that are already set up for your industry. Our network of partnerships throughout the Dallas area can link the right developer to the right manufacturer that brings the most value to both parties. For new builds, we can help with site selection, equipment needs, employee training, efficiency and everything else your plant needs to succeed.
McCownGordon brings value to both developers and manufacturers by getting into projects early and planning ahead to avoid potential problems down the road.
Learn more about the manufacturing process at McCownGordon from packaging manager, Amanda Tran.
What should you consider in selecting a manufacturing site?
Site selection is much more than finding an empty plot of land or an available warehouse building. When planning for the location of your manufacturing plant, you need to consider every need (and every future need) of your facility.
The physical space
The most obvious piece to consider is the site’s physical space. Is there enough square footage for production, warehouse, and space for your support systems (payroll, security, maintenance, etc.)? Consider the amount of space you’ll need initially and how future growth and expansion would be possible.
When determining if a space can accommodate vertical or horizontal expansion, McCownGordon is here to help. Our experts view every project through a future-focused lens to set you up for success from the start.
Many clients have returned to McCownGordon one to two years after building their manufacturing plant because they are ready to expand. We can help you anticipate those needs and plan ahead asking probing questions in the design phase. For example, “will the electrical and control systems support an extra production line when it’s time to expand.” Planning the right infrastructure up front can help save dollars later. We’re your long-term partner and will continue to serve you after the manufacturing plant is up and running to assist with your needs and be prepared to make your future expansion a seamless experience.
Cost
Cost is one of the most important factors to consider in site selection. Beyond the hard costs associated with construction, several outside factors will impact the cost of your build and the cost of ongoing production, including:
Utility costs
Cost of labor
Taxes
Cost of transportation for materials
Geotechnical requirements (for example, soil conditions might affect foundation types)
Building codes
When local governments want to bring companies and jobs into their communities, they will often negotiate tax credits or offer other incentives to developers. Our teams understand the DFW market and can help navigate this complex process and maximize these incentives. When you use McCownGordon to assist with your site selection, you’ll feel confident knowing you will get the most value for your investment.
The local labor force
It’s necessary to evaluate the local workforce during the site selection process. Due to the short supply of skilled labor, worker availability will be a deciding factor for where you build. When evaluating the local labor market, you’ll also want to look at unemployment rates, the number of workers in similar jobs, and the pay range and benefits those workers receive.
If you need a site near universities with the right training programs for your industry, McCownGordon is on your side. We can help you select a prime location where skilled graduates are there to feed your plant.
Traffic and transportation
Local transportation and traffic will determine the speed you can receive raw materials and ship out your finished product. Consider how far you will be from your vendors and distribution centers. How will traffic and transportation affect the time it takes to get your product from manufacturing to the end user?
Utilities
Your manufacturing plant needs utilities to run smoothly. If a potential site does not have the necessary utilities to power your plant, you can quickly eliminate it from the list. Consider the availability and cost of electricity, natural gas, water, wastewater, and telecommunications for your industry.
Community preferences
Manufacturing plants can have a significant impact on the local community. It’s important to find a site that aligns with the preferences and values of the surrounding community.
Your plant needs long-term success. McCownGordon helps you achieve this by selecting sites that foster positive community relationships.
Where should I build in Texas?
If you are planning a manufacturing plant site in Texas, it can be challenging to decide where to build. Many clients ask if they should build in Houston, Austin, San Antonio or Dallas. The answer depends on your specific industry and its interaction with the factors described above. McCownGordon can help analyze each of these factors, providing a comprehensive breakdown to help make the site selection easy.
What makes site selection in DFW different?
The Dallas market differs from other big cities because it is driven by developers. The majority of manufacturing plants are greenfield facilities due to population growth, local schools and an affordable cost of living.
DFW has seen a large influx of the electric vehicle (EV) battery market. Many prominent car companies are adding EVs to their lines, which has resulted in a boon of battery manufacturing in Dallas and the surrounding area. There has also been an increase in facilities that produce raw materials for the EV battery.
Your project doesn’t stop at site selection
You need a partner that will be with you through every step of the process, not just your manufacturing plan site selection in DFW. At McCownGordon, we go beyond the scope of a typical design-build firm and serve as your full-service integrator to help your project run smoothly.
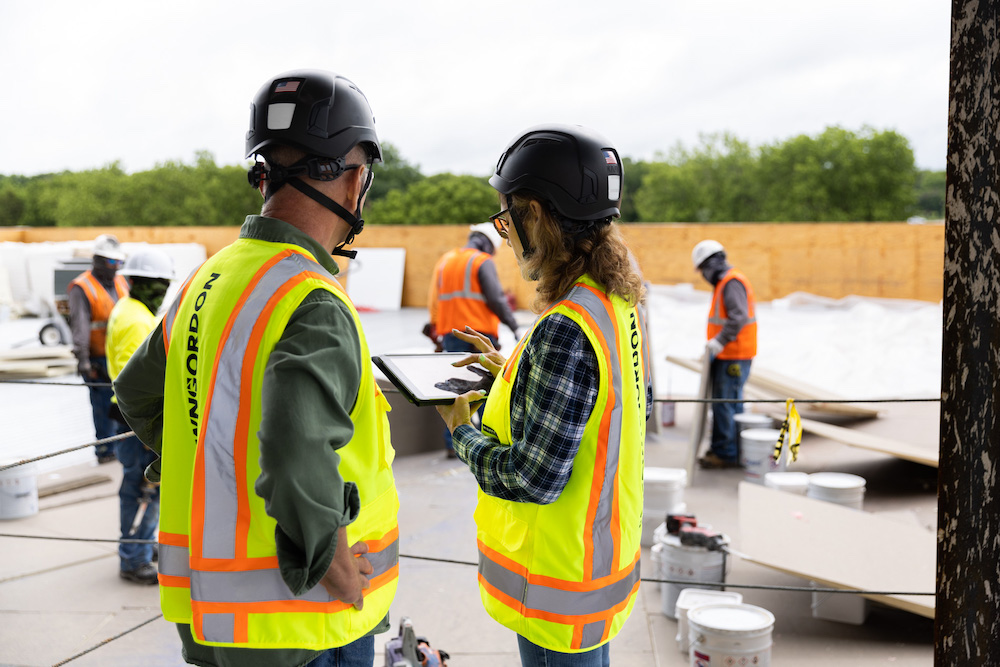
Maximizing efficiency
For existing manufacturing clients within 100 miles of DFW, McCownGordon can provide valuable insight with a facility audit. We complete a two-day, on-site investigation during the audit to assess all utilities, line efficiencies, control systems and equipment. Our experts will also review the flow of operators throughout the facility and will assess automated and semi-automated solutions.
Once the audit is complete, we create a detailed report covering safety changes, operator movement modifications, and equipment recommendations. When clients implement these changes, they often see a three to five year return on investment. Facility audits are low-cost upfront and provide significant long-term value for clients.
Simulation technology for analysis and training
Operator training is vital for safety and efficiency in a manufacturing plant. We use simulation technology, FlexSim to model, simulate and analyze equipment and different scenarios. FelxSim also adds the unique ability to help train workers to operate the equipment and prepare them before employees ever enter the facility.
A faster process
Our DFW leadership team has been serving the Dallas manufacturing market for more than 40 years. The relationships and connections we have developed over those years help us bring our clients’ manufacturing facilities to market quicker. Our integrated process eliminates the need for design to be 100% complete before issuing for construction and getting permits. We bring an improved turnkey approach of designing just a portion and then applying for permits, which allows you to break ground on construction much faster.
Aging Buildings
We don’t only help with new builds. If you’re a developer or owner that has acquired an older building, McCownGordon can help upgrade your existing facility to get it ready for a new tenant. No two tenants are alike, so we’ll help you select the best equipment and workflow for your needs. Using the latest technology, we create 3D models of the workflow to turn your aging building into an efficient and desirable manufacturing facility.
Construction Safety
Safety is a top priority through every step of the process at McCownGordon. Our associates adhere to strict procedures for construction site safety. We equip our team with ongoing training and up-to-date safety information to protect what matters most.
After the building is constructed, our safety program continues as we set up your building to adhere to safety standards, train employees to operate equipment safely, and ensure the safety of employees moving throughout the plant.
You need an experienced company for manufacturing plant site selection in DFW
McCownGordon is prepared to meet the needs for your manufacturing site in DFW and across all regions we serve. Collaborative project delivery methods lead to optimum results for nearly any project through reduced risk, early collaboration and balanced participation.
At McCownGordon, our team maintains a customer-focused mentality, allowing us to meet or exceed even your highest expectations. Dedicated to promoting integrity, performance and relationships, it’s our people and values that truly make the difference.
Our customers aren’t simply another project; they’re an extension of our team and community. Together, we don’t just build—we bring creative visions to life. From first thought to final implementation, we deliver quality work to ensure our builds stand above the rest.
We serve manufacturing clients nationwide with four regional offices—Kansas City, Manhattan, Wichita and Dallas-Fort Worth. Call us at 888-304-4929 or use our free online quote tool to start building today.